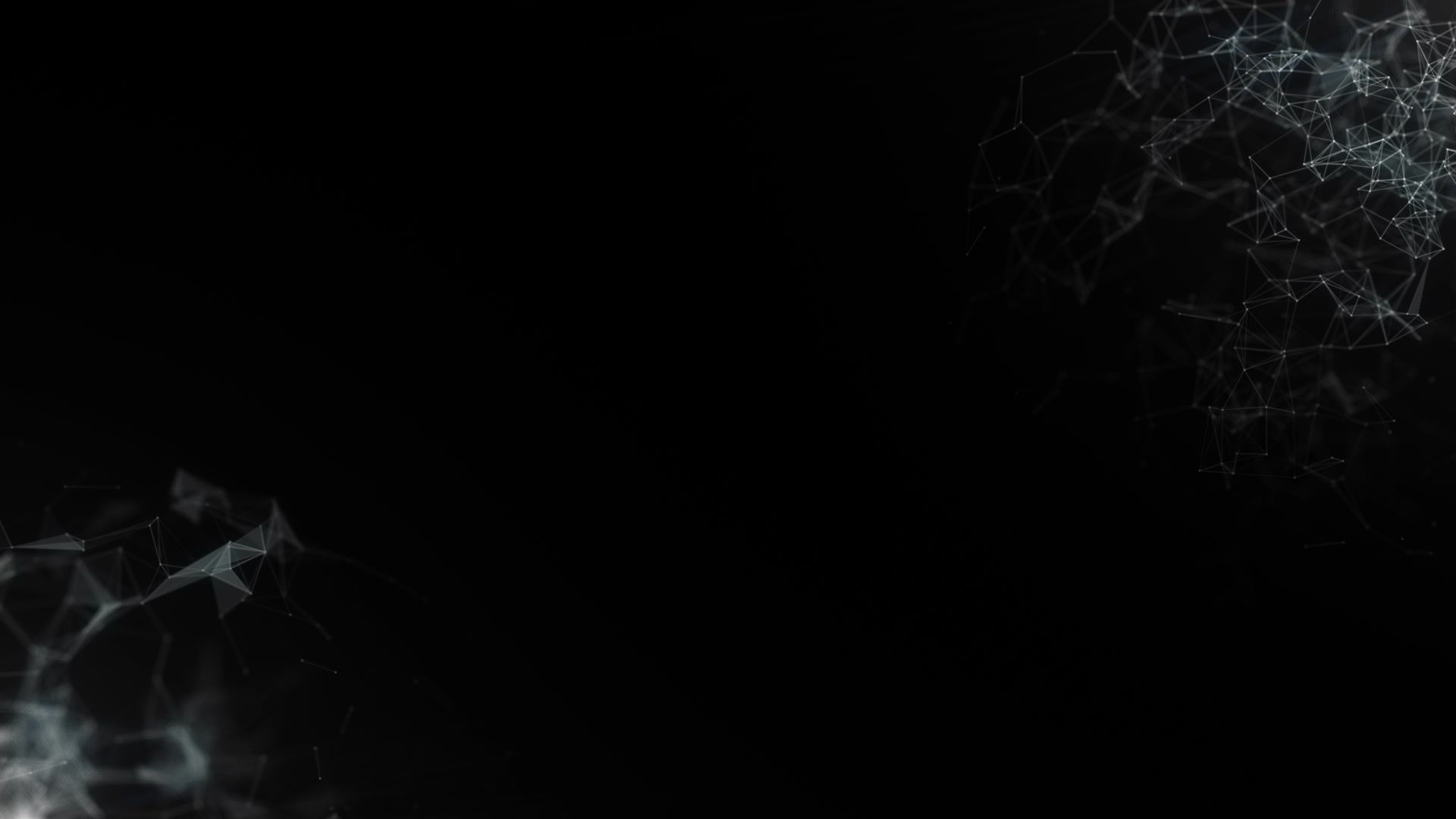
Riley Smith
Prosthetic Arm Structure
​
Motivation for this project is based in the current status of the prosthetic industry. In terms of how developed robotic prosthetics currently are, they use technology like myoelectrics for power and materials like carbon fiber. These systems and materials are generally expensive which makes them unavailable for most amputees. This device is designed to take cost-effectiveness into account with the use of plastics and an affordable form of actuation.
A device is needed that will provide an alternative option of a prosthetic for amputees. The necessary structure of this device must contain the actuation components provided.
Design Requirements:
-
Modeled structure is able to withstand 100 pounds of weight.
-
Device is designed with 2 articulation points in mind (fingers, thumb).
-
Each finger must have 3 points of natural motion, and the thumb 2 points in order to reach a natural position.
-
Limit tabs of the finger joints must be 1/16” thick
-
Pins at joints must have a 5 thousandth tolerance in order to have resistance free motion
-
The hollowed center of the palm must have a shell thickness of 3/16”
Engineering Merit: The arm structure will be designed in SolidWorks with the actuation hardware in mind. The necessary calculations will include the stress on the various joints that may fail in certain designs. An example of this is the forearm needing to support a 100 pound weight. That will depend on the material properties of ABS and PLA plastics, as well as the stress the forearm can withstand based on the applied load. Other necessary calculations include the reactions due to a 100 pound load, and being able to measure the capable grip pressure of each finger or the whole hand.
Scope of Effort: With two individuals working together on the structure and movement, this project stays within the necessary scope of the course. The most time spent on the project will take place during the design and testing portion, where the structure and actuation come together, and necessary changes will be made in order to achieve what is desired. The quantifiable effort will be a total of 12 hours a week at minimum until desirable function is attained.
Success Criteria: The device functions like a comparable prosthetic on the market with its similar points of articulation and the pressure that the hand can grip with. Common equations used within the analysis of the structure are the stress equations in both normal and shear. These equations include:
σ = Mc/I τ = V/A τ = VQ/It

ABOUT SKYLINE
I'm a paragraph. Click here to add your own text and edit me. It’s easy. Just click “Edit Text” or double click me to add your own content and make changes to the font. I’m a great place for you to tell a story and let your users know a little more about you.