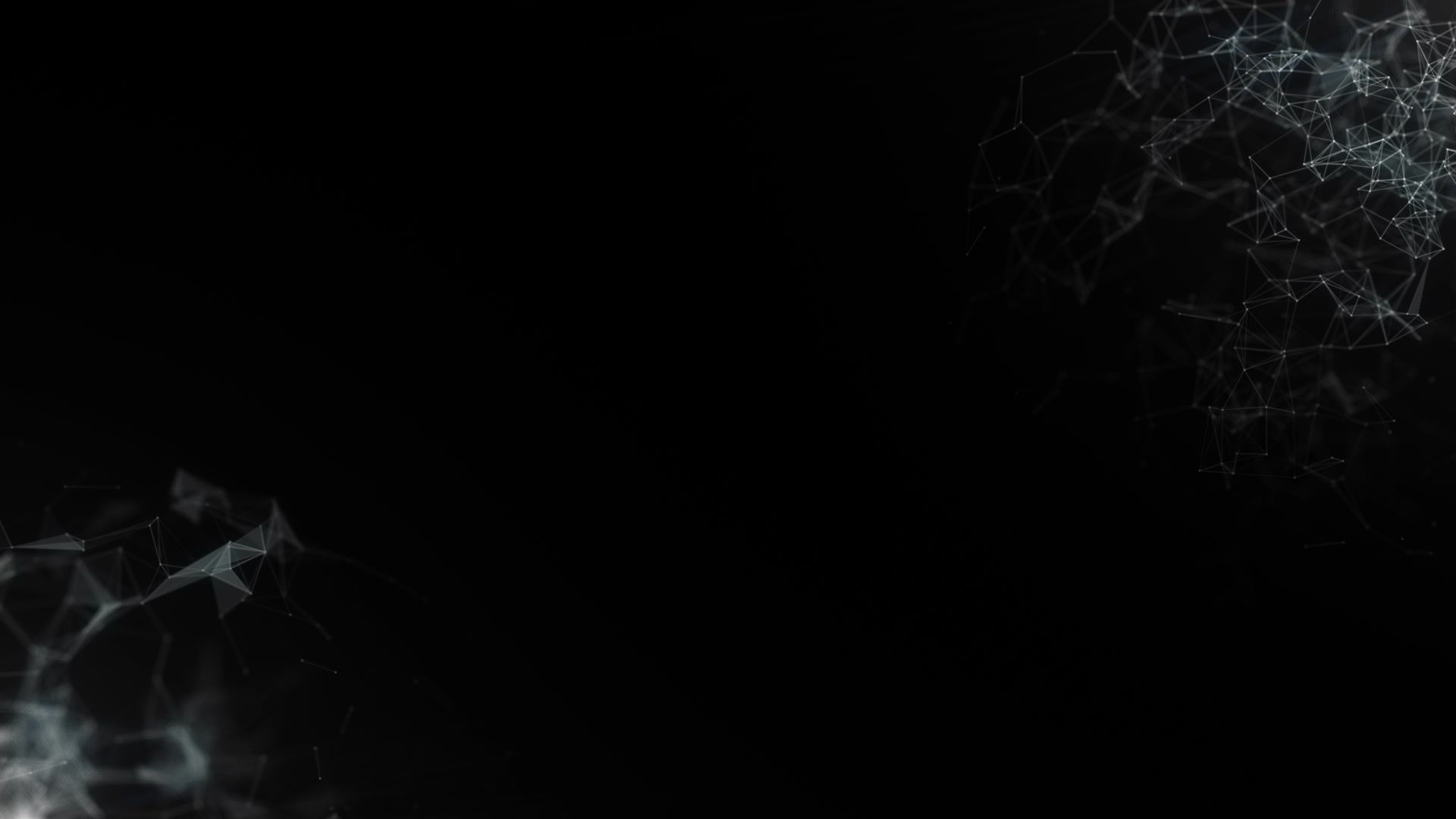
Riley Smith
Design and analysis:
The approach taken in this project is to produce an articulate hand through iterative designs. It will begin with a base structure and refine through each iteration until the result reaches what is desired. Each design iteration will be 3D printed and tested for fit and function so that revisions can be made for the next variation. The chosen style in how this hand is designed is meant to emulate human dimensions as closely as possible so that when it is in use, it looks proportionate to the human body.
In order to confirm that the hand produced is competitive in design, it will be compared to the Bebionic prosthetic in both articulated function and design proportions. The manner in which that prosthetic moves is the benchmark on which this project is aimed toward.
In terms of initial performance of the hand, it is expected that some structural components may fail once they are put into function or the test load from analyses is placed on them. This will lead to some redesign in order to optimize the components an avoid failure. There may also be cases where material choice can be changed due to observations once the components are produced.it may be seen that certain components printed in ABS do not need to be as rigid, so they can instead be made out of PLA.
Analyses necessary for the structure design in the project include calculating bending stress, shear, and torsion on the different components of the hand and in different locations on each. Some may be an analysis on some small element like a tab or hole. Others may be the whole component tested in shear to see what sort of safety factor is involved in the design.
Analyses
A-1: This analysis involves the necessity of a “limit tab” in the design of the fingers. It is proposed that without this tab the joints may return to an over-centered state once actuated back to rest. The calculation used involves a worst case load located on the fingertip so that the limit tab is tested to its maximum. The parameter found through the analysis is the necessary thickness of the limit tab at that load in order to prevent failure. The initially assumed thickness is 1/16” which works out to be just barely insufficient at a stress of 6009 psi compared to the flexural strength property of 6000 psi. This feature can be found in the drawing B-1.
A-2: This analysis is of the pins that hold each finger joint together. The requirement for the pins is to be able to withstand a 50 pound shear. the analysis done calculated the shear to be 4074 psi, which is less than the flexural strength of ABS so that means a pin diameter of 1/8”is sufficient. Also it means that the pin can be made of ABS if desired. There is not a drawing to represent this analysis.
A-3: This is an analysis of a potential palm movement tab that may be used in the case of articulating the palm if necessary. The tab needs to withstand a 5 pound shear load from the articulation. The analysis found that the tab can be 1/8” thick and be plenty sufficient. This analysis is not related to a drawing.
A-4: This analysis is of the palm as a whole. The requirement of the palm is to be able to withstand a 50 pound load in bending based on its supplied human scale dimensions. The analysis found that if the palm has the dimensions of 3 X 3.5 X 1 (LxWxH) then it can withstand the load with an ample safety factor above 100. The current design of the palm has changed to where it is 5 inches wide instead of 3.5, and this can be seen in drawing B-3.
A-5: This analysis is specifying the tolerance on the pins that assemble the joints. The requirement of the pin is that it possesses a tolerance more loose than 1 to 2 thousandths so that the hand joints can move freely without the restriction of friction on the joint. The analysis referenced our machining texts from basic machining and the text specified a tolerance of 5 thou to represent the fit. It was also tested on a display of fit tolerances and 5 thou was the exact fit desired. This tolerance is specified in the design of each joint on the hand.
A-6: Analysis 6 began as a search to find a source that states the maximum strength of ABS glue which was not a searchable property. In the design of the hand it may be necessary to split the finger joints in order to incorporate the actuation components. In order to fuse the halves together ABS glue will be needed so the maximum load it can withstand would be a necessary property. Since the glue is considered permanent, there is no discernable limit for the glue to possess.
A-7: This analysis is of the palm in a hollowed out state for weight saving and housing components. The 100 pound test load is used in a bending form to find the thickness of the palm shell without failure. It was calculated through flexure formula that a wall thickness of 3/8” would provide an ample safety factor of 10 to the palm. The hollowed palm analysis is not related to a drawing.
A-8: This analysis is of the finger joint mounting points and if their dimensions are sufficient. The fixture points need to withstand a 100 pound load as a worst case. The analysis did calculations in shear, torsion, and bending. It was calculated that the tabs could withstand bending with a safety factor of 1.7, but the torsion was at a safety factor of 0.5 or less. Fixture points are visible in all current drawings.
A-9: This analysis is of the redesigned upper finger joint based on the 100 pound test load. The designer of the actuation components needed force in a particular axis to determine if the actuation cam pins will have sufficient size. The force in the direction of shear was needed and it was found to be 80 pounds. The drawing of the upper finger joint can be found in appendix B as B-6.
A-10: This analysis is of the lower finger joint since it is required to be hollowed out to house actuation components. The analysis for the joint was to find the available inner area of the joint so that parts for motion can be contained. The parameter found was that the inner area available with a 1/16” wall would be 0.625 inches. There is not a drawing to represent the dimension found.
A-11: This analysis determined the amount of shear on the upper finger joint due to the 80-pound force component in the shear direction. This value was determined in A-9. The direct shear calculated was 142 psi, which would not result in failure when the flexure modulus of ABS is 6 ksi. The drawing B-6 displays the design of the upper finger joint.
A-12: This analysis is based on the wall dimensions of the lower finger joint discussed in analysis A-10. In order to test the wall thicknesses of the joint, a single side was modeled as a short column. Using Eulers equation the buckling load was found to be 10385 pounds, which seems very high but shows that the thickness of the shelled joint would not induce bucking when facing a 100 pound load like the previous analyses.